Small Components with a Big Impact
Electronics play a crucial role in today's industry and modern production processes would be unthinkable without them. It enables the automation and optimization of production and manufacturing processes. Electronic systems and sensors monitor and control machines, improve the precision and quality of manufactured products and at the same time minimize energy consumption and operating costs.
This makes it all the more important to ensure that the electronics used are working optimally. This is where kolb Cleaning Technology GmbH comes in. kolb is an international full-service provider of cleaning systems, cleaning chemicals, technology, process and software design for the electronics manufacturing industry. The company manufactures machines and cleaners for large and wellknown global customers, ensuring the optimal use of electronic components in industry and private use. With a high level of in-house expertise, kolb covers all processes involved in the cleaning of electronic components and is at the forefront of innovation by using new technologies and placing a high value on sustainability.
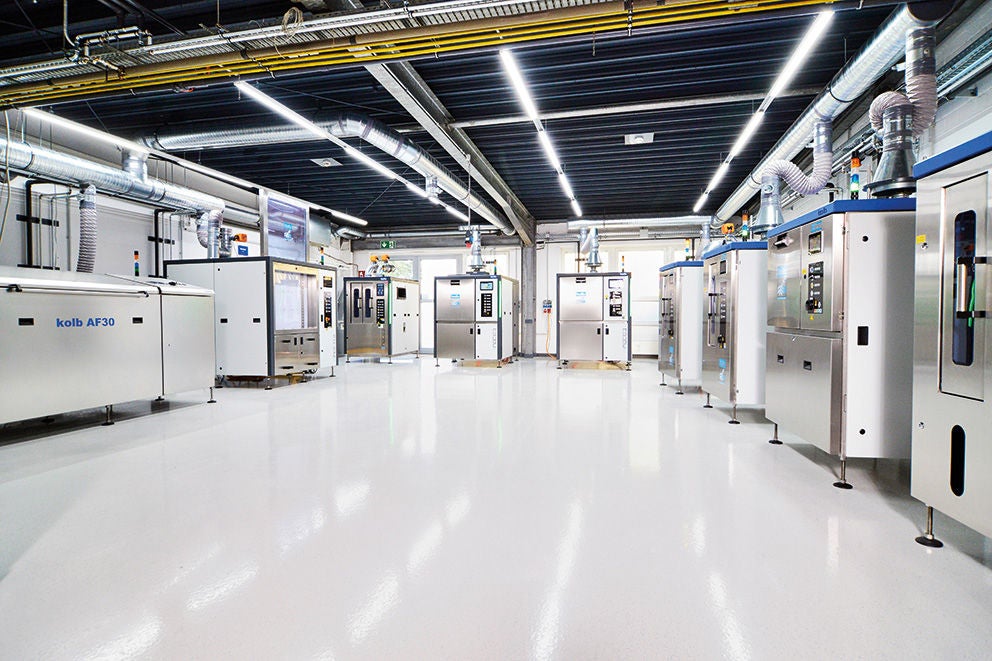
From Paper Drawings to the Digital Catalog
kolb and Cideon have been working together successfully since 2011. Christian van der Stein, Head of Product Management at kolb, recalls: “Back then, we decided to design exclusively in 3D. We implemented Autodesk Inventor and Autodesk Vault Professional as well as various smaller programs. Since then, I have been in regular contact with Cideon whenever we need something.”
The request for a digital spare parts catalog came from the customers. “Until now, we have provided printed PDF lists of our spare parts. Of course, we kept an eye on what was happening in the market and what our customers were telling us. There are VR goggles that allow you to look inside a machine and see what spare parts are available. That's great at a trade show, but not necessarily practical for everyday use. We wanted a pragmatic solution that would keep the workload and costs within reasonable limits,” explains Christian van der Stein.
Around the same time, Cideon also came up with the idea of using Autodesk Platform Services (formerly Autodesk Forge) to develop a digital spare parts catalog as a standardized product that directly reuses our customers' existing data. As part of the portfolio process, a workshop was organized in the summer of 2022, attended by four selected Cideon customers. Due to the COVID-19 pandemic, the workshop was held online. “The aim of the workshop was to find out what pain points customers have in the area of spare parts sales. Of course, we had already thought about what our customers might need, and the input from the workshop was very much in line with what we ended up developing as a product," says Cideon Portfolio Manager Benedikt Sigg.
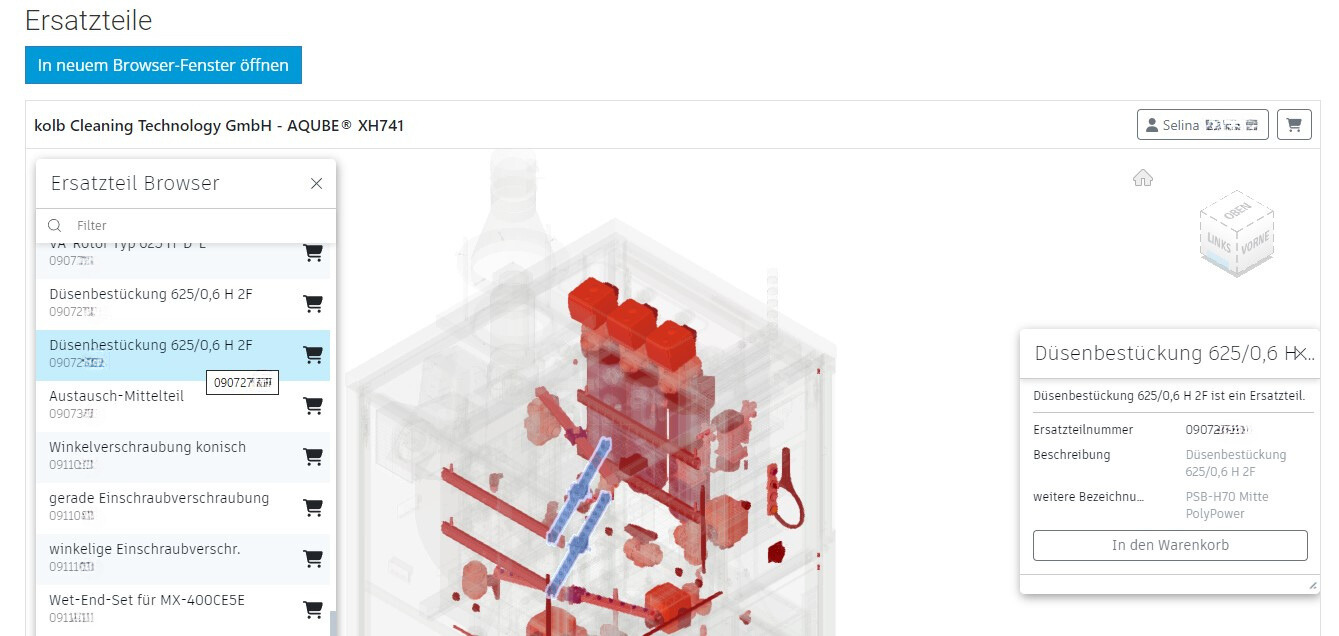
Proof of Concept for the Trade Show Presence
“As the product development of Cideon Sparify progressed in mid-2023, we approached all four customers from the online workshop. kolb immediately picked up the thread and had the idea of using it to build their own service portal for their trade show presence. They had an immediate vision of how they wanted to use Sparify,” recalls Sebastian Cordes. Christian van der Stein adds: “Our expectation was that we would be able to visually present the 3D models already created for production on a platform in such a way that allows our customers to see at a glance what they could order as a spare part.”
In fall 2023, kolb attended the 'Productronica', the most important international trade show for the electronics manufacturing industry. The goal was to set up a proof of concept (PoC) with Cideon Sparify before the trade show. Many existing customers were present at the trade show to ask about new products and the new platform was presented. At this point, the solution was already configured as it is used today, but some technical details were still missing.
Christian van der Stein quickly realized that kolb wanted to continue using the solution: “Customers really liked the spare parts catalog. Many of them said that they finally no longer had to search for pictures and mark them with an indicator to select spare parts. Now they can click on the part they want, put it in the shopping cart, and get a quote.”
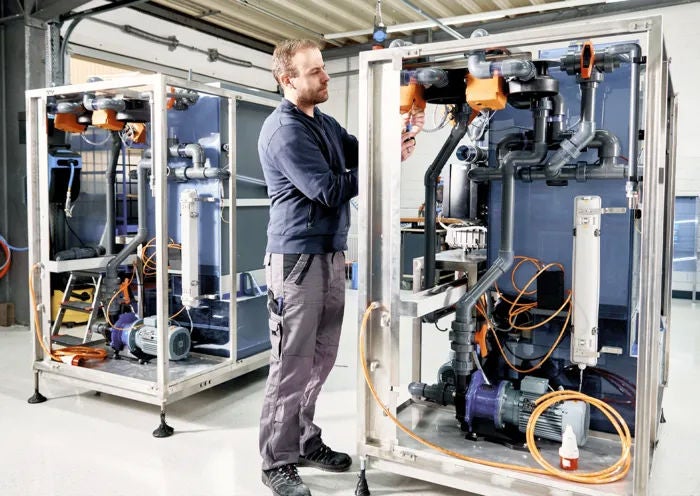
Read more about the project between kolb Cleaning and Cideon in the reference report:
How do you become a Cideon reference customer?
Are you currently working successfully with us on a joint project? Each of our customers is individual, has specific requirements and therefore very different solutions that are implemented. For us, every customer project is unique and should be valued just as much.
In our reference reports we focus on your company, the project highlights and your benefits.
Would you like to present your company and the joint project even more prominently? Then simply contact your responsible Cideon Account Manager and we will take care of all the further details for creating a reference report and publishing it on our website, blog and social media.